Health and Safety are key priorities at the Caribbean Cement Company, and have been reinforced by significant investments in training, equipment and improved processes. The result has been the mainstreaming of a safety culture throughout the organisation which has manifested in a track record of 1,832 days without lost time injuries (LTI) at the quarries and 1,008 days at the plant among permanent employees as at the end of June this year. Within this was the achievement in July 21 of a special milestone of 365 days LTI free across all areas of the operation.
Physically reshaping the plant is also a key priority. From signage, to the creation of pathways, the installation of new, state-of-the-art equipment and demolition of obsolete structures, the landscape is being redesigned for optimal safety. Among the initiatives undertaken in recent years was the demolition of nine large, obsolete structures such as mills, burner buildings and conveyor structures. This was a mammoth execution which was successfully completed and has significantly improved the safety, environment and aesthetics of the plant.
To further entrench a safety mindset, all employees have participated in 52 hours of training in the CEMEX Health and Safety Academy. The mandatory three-module interactive workshop gives a framework to deal with all categories of risks encountered on the plant. This workshop is in addition to daily safety talks and other behaviour promoting tools. CEMEX is a global building materials company of which Carib Cement is a member.
“Carib Cement has a lot of experience in safety and implements the industry’s highest standards at our plant. We have invested at least USD50 million in the last three years to improve production and safety. Our goal is Zero for Life, which means a totally incident free environment and our team is committed to that objective. Now, with the onset of COVID-19, we continue to focus on creating a safe zone where our employees who need to be physically at the plant can work safely with access to all the resources they need to protect themselves and each other,” said Yago Castro, General Manager.
Incorporated within the company’s safety initiatives are 52 new protocols developed by CEMEX to help employees, their families, customers and community members mitigate against COVID-19 risks and flatten the curve. These protocols complement other measures such as the introduction in March of: temperature checks on entrance, hand-free sanitisation stations, replacement of palm-in clocks to scanned tags, remote work, an app which allows cross-checking of symptoms, and paperless offices. The protocols provide guidance on all forms of interaction for everyone including, drivers, salespersons, and the operations teams. For example, protocols developed for truck drivers cover: Taking care of your family at home; Commuting and getting home safely; Loading and dispatch; while protocols for the sales team cover: Commuting to work, Behaviors in Office and at the Customer Site, Getting Home Safely, and Essential Travel.
“COVID prevention is the responsibility of every person, but companies especially have a responsibility to create a safe environment for their employees. Our team has been very responsive to the new protocols and we continue to reinforce their importance as this is key to our being able to maintain a COVID free environment,” Mr. Castro said.
*This article was featured in the Vision: The Change we Seek, a magazine published by the Jamaica Chamber of Commerce. Please click here to read the magazine
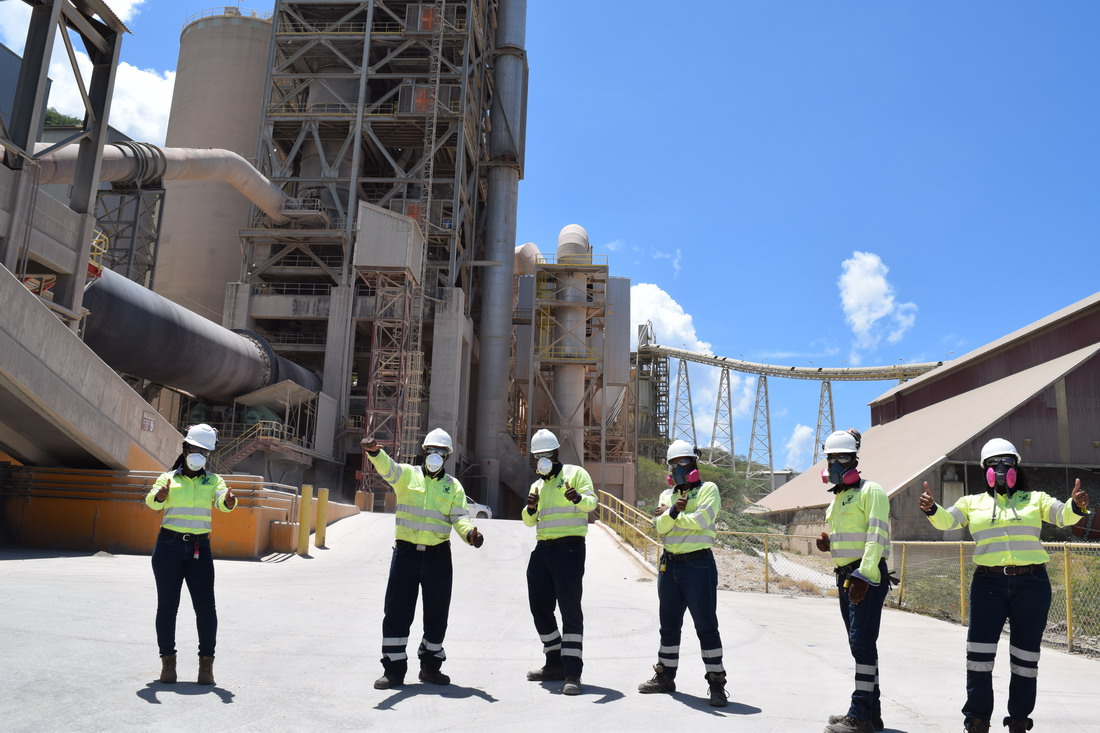